More Than Just a Production Line Upgrade, This is a Profound Transformation in Efficiency, Quality, and Future Competitiveness
HEFEI, ANHUI – [11/7/2025] – In today's China, every traditional industry faces the defining challenge of an intelligent transformation. For the labor-intensive grain and oil processing sector, this imperative is especially critical. Recently, a landmark project jointly completed by Zhangzhou Jialong Technology Co., Ltd. ("Jialong Technology"), a leading automated packaging solutions provider, and Anhui Winall Hi-Tech Grain and Oil Purchase & Sales Co., Ltd. ("Winall Hi-Tech"), a provincial benchmark in modern agribusiness, vividly illustrates the profound implications of this "intelligent manufacturing" revolution.
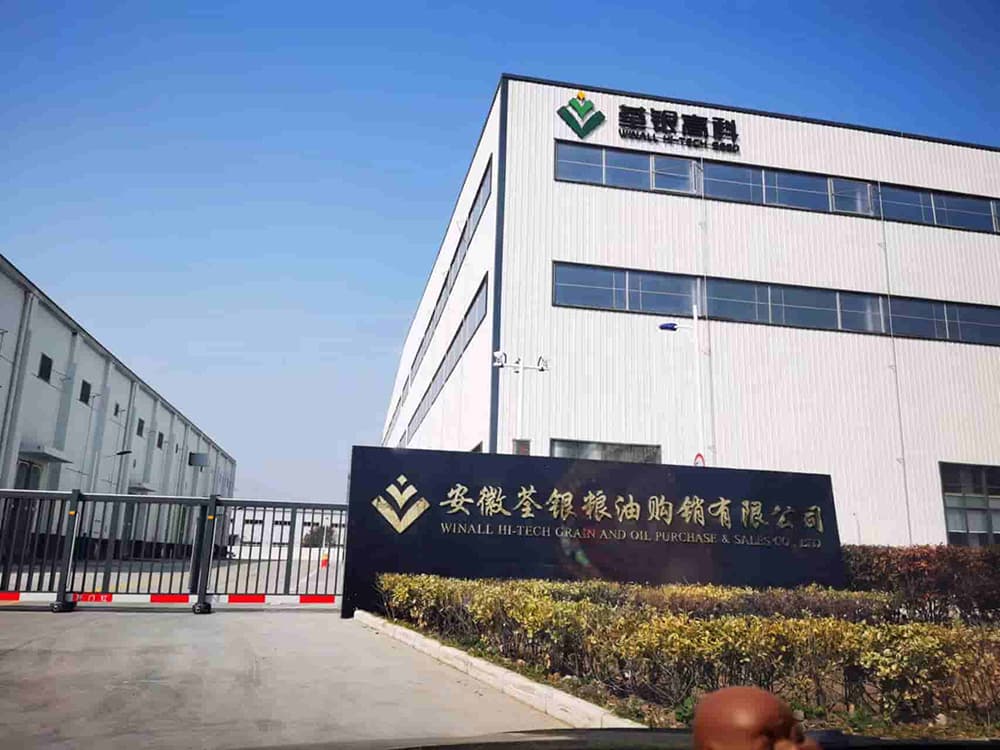
Act I: The Visionary in a Dilemma – Winall Hi-Tech's "Efficiency Anxiety"
"Our orders were growing, our market was expanding, but our production floor was increasingly resembling a 'battlefield'," recalls Mr. Wang, Production Manager at Winall Hi-Tech, describing the initial situation candidly. At the time, the company was in a period of rapid growth, but its traditional, manual-labor-dependent packaging model had become its Achilles' heel.
The challenges were threefold:
The Efficiency Bottleneck: The speed and consistency of manual bagging, weighing, sealing, and handling were limited, failing to match the capacity of the upstream production lines. This led to material backlogs and constrained overall output.
Quality Fluctuation: Manual operations inevitably led to inconsistencies. The weight accuracy, seal aesthetics, and stability of stacked pallets were difficult to standardize, which subtly eroded the consistency of their brand image.
The Management Pain Points: Difficulties in recruiting, rising labor costs, high employee turnover, and complex on-site management were constant pressures weighing on the leadership team.
The management at Winall Hi-Tech astutely recognized that to win the future, they had to fundamentally change their mode of production. They didn't just need new machines; they needed an intelligent, integrated system capable of reshaping their entire packaging workflow.
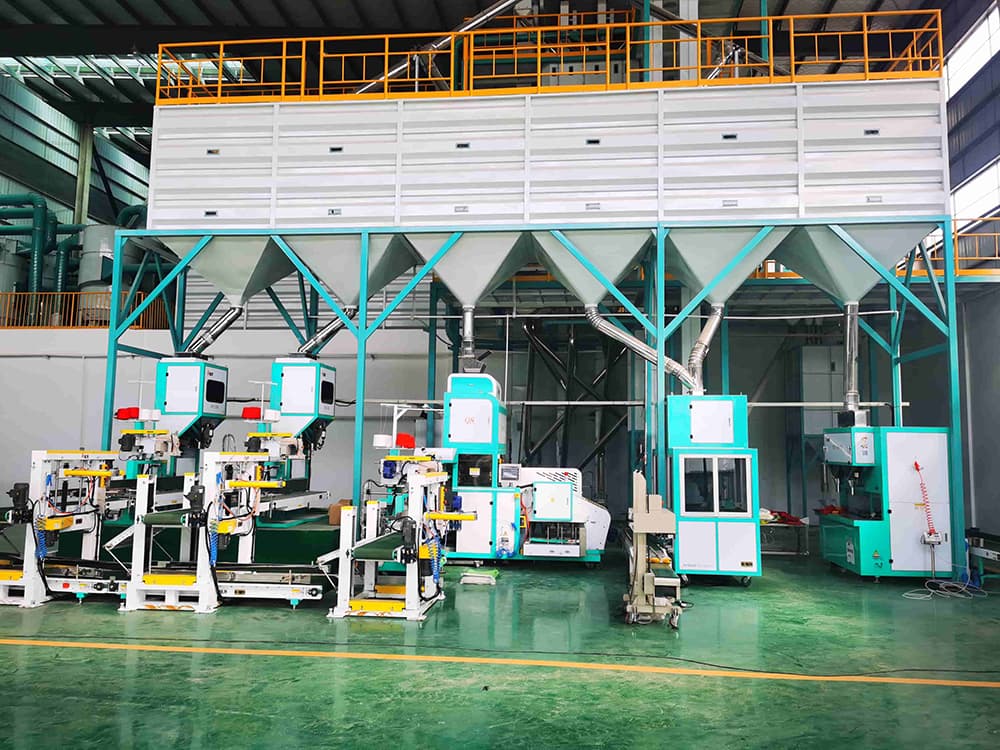
Act II: The Game Changer's Answer – Jialong Technology's Customized "Surgical Precision"
Tasked with solving Winall Hi-Tech's challenge, the Jialong Technology project team arrived on site. Like a skilled surgeon, they meticulously diagnosed every "nerve ending" of the production process.
"Our core philosophy is 'seamless integration, maximum value,'" explains Mr. Chen, Project Director at Jialong Technology. "The first thing we did was listen, not sell. We realized the client's pain points weren't just about being 'slow,' but about the countless points of friction throughout their workflow."
Jialong's proposed solution was a masterstroke of engineering, built on three pillars: Automation, Digitization, and Intelligence.
Process Automation & Reinvention: They designed more than just isolated pieces of equipment; they engineered a cohesive "data flow" and "material flow." The journey of the material was carefully orchestrated: descending from the silos into a matrix of LCS-series high-precision weighing and packaging machines for rapid, accurate filling and sealing; proceeding through a custom-designed shaping and accelerating conveyor belt to uniform the bag shape for perfect robotic handling; and finally, arriving at the line's heart—a high-performance white Kawasaki robot. This robotic arm executed its pre-programmed palletizing routines with almost artistic precision.
Operational Digitization & Transparency: The central control system did more than just set and switch packaging parameters. It provided real-time monitoring of each machine's status, production rates, and predictive maintenance alerts, transforming the once-opaque production process into a transparent, quantifiable operation.
Decision-Making Intelligence & Support: The Kawasaki robot was more than just a "lifter." Its advanced algorithms allowed it to automatically optimize gripping paths and stacking patterns for different product specifications, maximizing pallet stability and space utilization. The entire line was protected by an intelligent safety system of light curtains and interlocked fencing, ensuring safe human-machine coexistence.
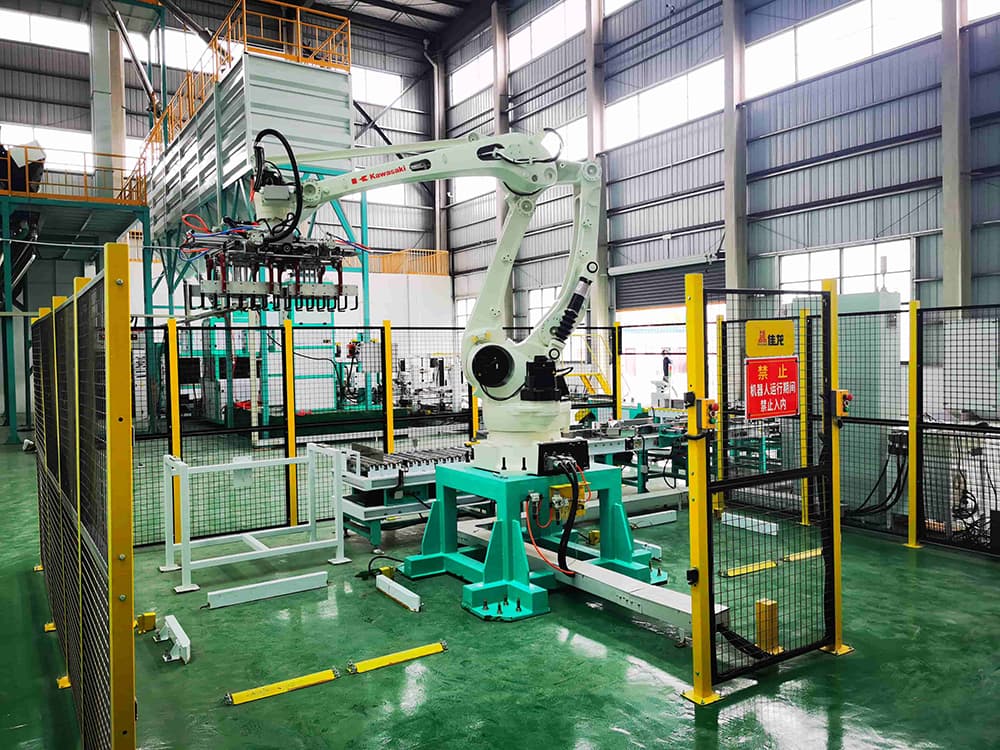
Act III: A Rebirth Through Transformation – Tangible Benefits, Palpable Value
When the new line went live, the change was revolutionary.
Mr. Wang shared some figures with evident delight: "Our single-line packaging capacity increased by nearly 300%, while our on-site operator requirement dropped by over 70%. But that’s not all. The most satisfying part is the 'certainty' we've gained. Now, the weight of every single bag is accurate to within a few grams, and every pallet looks like a perfect clone of the last. Our warehouse manager jokes that the warehouse is now more orderly than a military parade!"
This transformation went beyond production data, permeating the company culture. Employees were liberated from strenuous manual labor, transitioning into skilled technical roles monitoring and maintaining equipment, enhancing both their work environment and their sense of personal value.
"With this investment, we were focused on long-term, comprehensive returns," Mr. Wang concluded. "What Jialong Technology delivered was not just a set of machines, but a modern production philosophy and management model. It has given us a stronger footing and a brighter future in a fiercely competitive market."
This collaboration stands as another testament to Jialong Technology's customer-centric, value-driven service philosophy. It provides a powerful and compelling case study for how China's traditional industries can achieve a magnificent leap from conventional to intelligent manufacturing through the fusion of advanced technology and deep industry insight.